Quality Assurance vs Compliance: What’s the Difference
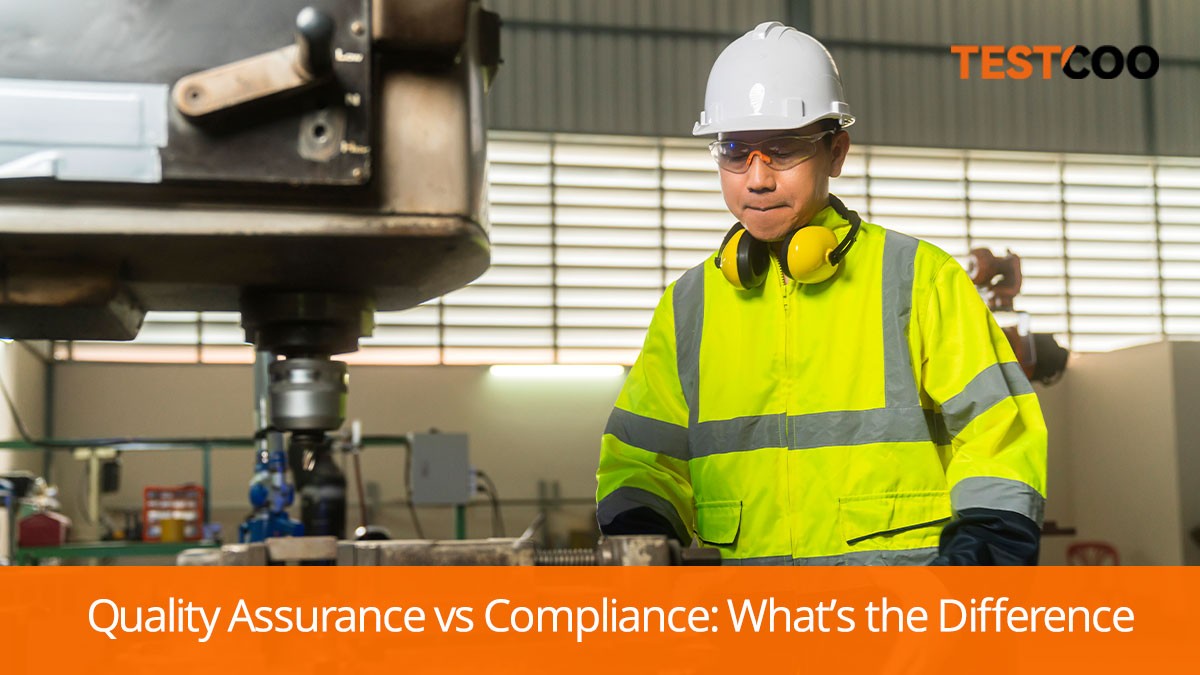
Quality Assurance and Compliance are critical for companies manufacturing consumer products. QA ensures that products and services meet high standards of quality, while compliance is about meeting regulatory requirements.
If you want to manufacture competitive products, operate profitably, and grow your business, you must pay attention to both. Together, they help build trust, reduce risks, and enhance overall organizational performance.
In this article, we'll talk about the difference between quality assurance and compliance.
What is Quality Assurance?
According to the ISO 9000 Family of standards clause 3.2.11, Quality Assurance is defined as "A part of quality management focused on providing confidence that quality requirements will be fulfilled." It involves planning, documenting, and agreeing on a set of standards to assure quality.
Quality Assurance is a clear and concise framework that embraces every element of the operations of an organization, not least quality management which plays an instrumental role in fostering a culture of constant, ongoing improvement. The QA team is involved in all stages of development: production, testing, packaging and delivery.
The primary aim of QA is to reduce the risk of defects – and importantly, to address faults as early as possible in the value chain. In practice, this means putting in place both technical and managerial processes, so as to efficiently monitor and improve product or service quality.
This involves the production process being monitored to make sure everything is carried out how it should be to ensure the highest quality of product. There might be tests, assessments and observations made to improve the quality through that process meaning a better standard is being strived for.
QA also ensures compliance with industry standards and regulations, gives organizations a competitive edge, and directly contributes to higher profitability.
Best practices in quality assurance
Quality assurance retains its magic when implemented in alignment with a series of best practices, including:
- Strong leadership commitment and support
- Detailed quality planning in product design and process development
- Comprehensive training on QA principles and procedures
- Rigorous process documentation and control
- Extensive collaboration and communication across teams
- Ongoing audits and risk assessment
- Use of statistical quality control tools
- Validation of corrective/preventive actions
- Continual measurement and analysis of quality data
- Recognition and replication of best practices
Close adherence to best practices ensures the integration of quality into every step of the value chain, from R&D to procurement, production to distribution – and all the way to post-sales services.
What is Compliance?
The definition of compliance is “the action or fact of complying with a wish or command.” Compliance refers to the process of ensuring that an organization adheres to external laws, regulations, industry standards, and internal policies. It involves following the rules and guidelines set by governmental bodies, industry groups, or the organization itself to avoid legal penalties, financial losses, and reputational damage. Compliance is essential for maintaining the integrity, safety, and ethical standards of companies and manufacturers.
For example, selling clothes in America, the CPSIA requires that adult apparel and children's sleepwear must comply with labeling requirements, fire safety standards, chemicals, heavy metals restrictions, and other rules. Selling unsafe and non-compliant products is not only a severe risk for the consumers in your target market, but also something that can massively backfire on your own business. Your products may be subject to a forced recall.
Product compliance is essential to doing business, and it is vital to research all regulations that apply to your product thoroughly. Otherwise, you are putting your company at risk and making adverse business outcomes more likely.
Ensuring Quality Compliance
There are a number of ways companies meet compliance requirements. Firstly, they need to understand what is expected and the rules that have been set, next they need to abide by them by observing and reporting on performance. If they aren’t complying with the standards, something needs to be done to rectify that and resolve the issues.
In short, compliance ensures a manufacturer or supplier of a product meets the requirements of accepted practices, legislation, prescribed rules and regulations, specified standards, or the terms of a contract.
The Difference between Quality Assurance and Compliance
Quality Assurance (QA) and Compliance are two distinct but related concepts in the realms of business, manufacturing, and service industries. Here's a detailed comparison:
Quality Assurance aims to ensure that a product or service meets specified requirements and standards and focuse on improving processes to prevent defects. QA involves the development and implementation of systematic activities and processes to ensure quality and covers all aspects of production or service delivery, including design, development, production, and maintenance.
Compliance aims to ensure that an organization adheres to external laws, regulations, and standards and focuses on meeting legal and regulatory requirements. Compliance involves adhering to established rules and regulations set by external bodies and relate to particular laws, regulations, or standards that apply to the industry or sector.
Key Differences
Objective:
- QA is about improving the quality of products and services to meet customer expectations.
- Compliance is about meeting legal and regulatory requirements to avoid penalties.
Approach:
- QA is proactive and focuses on continuous improvement and preventing defects.
- Compliance is reactive and focuses on adhering to specific rules and regulations.
- Scope of Influence:
- QA covers internal processes and the overall quality management system.
- Compliance deals with external regulations and standards.
Focus:
- QA is customer-oriented.
- Compliance is regulatory-oriented.
Both QA and compliance are crucial for organizations to operate effectively and sustainably. QA ensures products and services meet quality standards, while compliance ensures adherence to legal and regulatory requirements. Together, they help maintain a company’s reputation, customer trust, and legal standing.
TESTCOO Helps you Manage Quality and Compliance
To succeed, you need both quality assurance and compliance working together. Quality assurance ensures that your products or services consistently meet high standards, while compliance keeps you on the right side of the law. By combining these two approaches, you can improve efficiency, reduce risks, and ensure customer satisfaction.
If a company strives for higher quality and provides assurance to its customers, its products and services will continually improve. By complying with industry standards and regulations, the company not only adheres to legal but also ensures its products and services meet industry requirements.
There are, of course, many different things to consider when thinking about quality assurance and compliance. That’s why TESTCOO-a third-party quality partner makes sense to offer information, assistance and options for your business. It makes sense to make sure you are doing everything you can to provide the best to your end consumer and that you meet regulations and standards set by your industry.
Contact us today!
Free Sample Report Performance Quality Control
Download a sample report to keep control of your supply chain!
Featured Articles
- AQL Table | How to Read It
- TOP 10 Common Defects in Garments Quality Inspection
- Product Packaging and Shipment Label requirements for Amazon FBA
- What Is ASTM-F2413-18? Protective Footwear Standard
- How to Conduct Third-Party Quality Control Inspections for Electric Scooters
- SMETA Audit-What is SMETA Audit?
- TESTCOO Supplier Verification/Certification Service SLCP, Higg FEM, GRS, GOTS
- Quality Control Inspection Company in China
- What is Quality Inspection? A Complete Guide
- Guidelines for Product Inspection in India
Category
- Production Inspection Service
- Factory Audit
- Softline Inspection
- Hardline Inspection
- Electrics Inspection
- Certification
- Checklist
- Manufacturers
- Quality Assurance Basics
- Products Recall
- AQL
- Guidence and Standard
- News
- Supplier Management
- Amazon
- Protective Equipment
- e-commerce quality control
- Indian Manufacturing
- Soft Goods Quality Control
- Supply Chain Management
- Supply Chain Resilience
- E-Commerce Quality Control
- ISO 2859
- Supply Chain Optimization
- Garment Industry
- Higg Index